Quality control in CNC metal parts production is paramount for ensuring the highest standards in manufacturing. For businesses in the industry, stringent quality control measures are not just a regulatory requirement but also a competitive advantage. This blog post dives deep into the importance of rigorous quality control in CNC machining, key quality control measures, consistency in quality assurance, and the role of inspection and testing in manufacturing CNC metal parts. By the end of this post, you'll have a comprehensive understanding of how to maintain and improve the quality of CNC machined components, giving your business the edge it needs.
Table of contents:
The Importance of Rigorous Quality Control in CNC Machining
Key Quality Control Measures for CNC Metal Parts
How to Ensure Consistent Quality in CNC Machined Components
The Role of Inspection and Testing in CNC Metal Parts Manufacturing
The Importance of Rigorous Quality Control in CNC Machining
Ensuring the quality of cnc machining metal parts is critical to maintaining customer satisfaction and product reliability. Rigorous quality control reduces the risk of defects, which can lead to costly recalls and damage to the company's reputation. Additionally, high-quality products result in fewer returns and complaints, enhancing customer trust and loyalty. In a market where precision and reliability are crucial, implementing stringent quality measures can set a business apart from its competitors. Therefore, investing in advanced quality control systems is not just an operational necessity but a strategic business move.
Key Quality Control Measures for CNC Metal Parts
Effective quality control in CNC machining involves several key measures that ensure each part meets the required standards. First, implementing tight tolerances through precision machining is essential. This means using high-quality CNC machines that can consistently produce parts to exact specifications. Second, regular calibration and maintenance of CNC machines ensure they operate at peak performance, reducing the likelihood of errors. Third, using high-grade materials and inspecting them before use helps prevent defects from the outset. These measures collectively ensure that the final product is of the highest quality, meeting both industry standards and customer expectations.
How to Ensure Consistent Quality in CNC Machined Components
Consistency in quality is achieved through a combination of robust processes and regular monitoring. Establishing standard operating procedures (SOPs) for every stage of production ensures that each part is made to the same high standard. Incorporating real-time monitoring systems can detect deviations from these standards, allowing for immediate corrective action. Employee training is also crucial; skilled operators are less likely to make mistakes and more likely to spot potential issues before they become problems. By fostering a culture of quality and continuous improvement, businesses can maintain high standards consistently.
The Role of Inspection and Testing in CNC Metal Parts Manufacturing
Inspection and testing are integral components of the quality control process in CNC machining. Visual inspections help identify surface defects, while dimensional inspections ensure parts meet specified tolerances. Non-destructive testing (NDT) methods, such as ultrasonic or magnetic particle inspection, can detect internal flaws without damaging the part. Additionally, hardness testing verifies that the material properties meet the required specifications. These inspections and tests are carried out at various stages of production, from raw material verification to final product inspection, ensuring that every part delivered to the customer is of the highest quality.
Quality control in CNC metal parts production is a critical aspect that can significantly impact a company's success. By implementing rigorous quality control measures, ensuring consistent quality, and conducting thorough inspections and testing, businesses can produce high-quality CNC metal parts that meet or exceed customer expectations. This not only enhances customer satisfaction but also provides a competitive advantage in the market. For businesses looking to improve their quality control processes, investing in advanced technologies and continuous training for employees is essential. Start implementing these practices today and see the difference in your production quality.
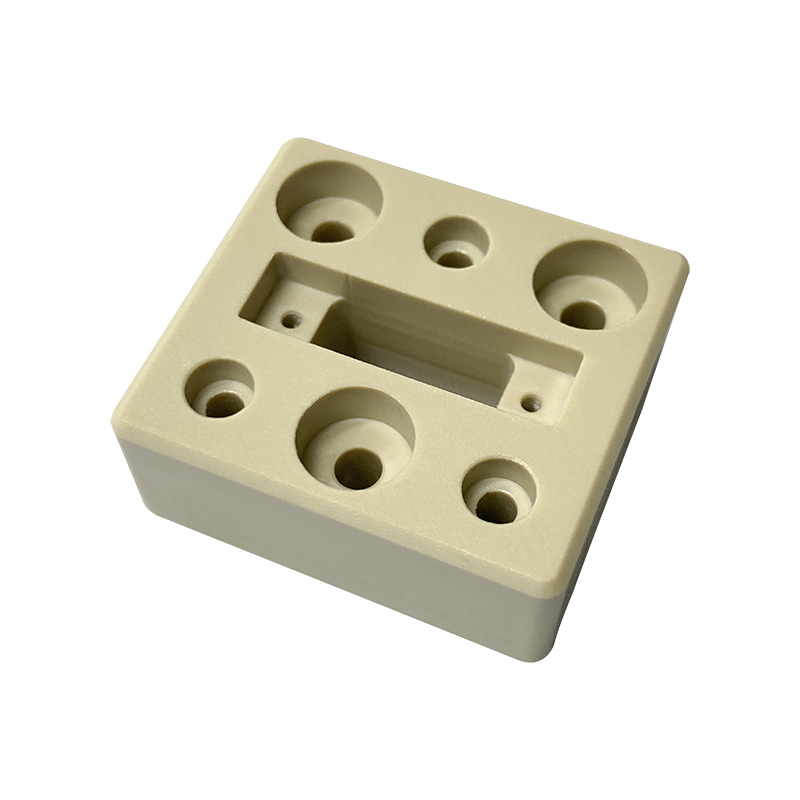
Comments
Post a Comment