In the world of advanced manufacturing and critical applications, the quality of materials can make or break a project. This is especially true for hafnium wire, a material prized for its high melting point, corrosion resistance, and reliability in demanding environments such as aerospace and nuclear reactors. Ensuring the highest quality in hafnium wire production is essential for achieving optimal performance and safety. But how can you be sure that the hafnium wire you’re using meets the stringent standards required? In this blog post, we'll explore the importance of quality control in hafnium wire production, the role of advanced manufacturing techniques, methods to verify purity and composition, and real-world case studies that demonstrate the impact of quality hafnium wire.
Table of contents:
How Strict Quality Standards Ensure the Reliability of Hafnium Wire
The Role of Advanced Manufacturing Techniques in Producing High-Quality Hafnium Wire
How to Verify the Purity and Composition of Hafnium Products
Case Studies: Customers Choosing Quality Hafnium Wire for Critical Applications
How Strict Quality Standards Ensure the Reliability of Hafnium Wire
Quality control in hafnium wire production begins with strict standards that ensure the material's reliability. These standards cover everything from the raw materials used to the manufacturing processes and final inspections. For instance, high-purity hafnium wire, such as that offered by Youtian Metal, adheres to ASTM B737 standards, ensuring consistency and dependability.Strict quality standards help prevent defects and impurities that could compromise the wire's performance. By adhering to these standards, manufacturers can produce hafnium wire that meets the exacting needs of industries where failure is not an option. This level of quality control is essential for applications such as control rods in nuclear reactors or components in aerospace engineering, where even the smallest flaw can have catastrophic consequences.
The Role of Advanced Manufacturing Techniques in Producing High-Quality Hafnium Wire
Advanced manufacturing techniques play a crucial role in producing high-quality hafnium wire. These techniques include precision drawing and rolling processes that ensure tight dimensional tolerances and consistent quality. For example, Youtian Metal employs state-of-the-art manufacturing techniques to produce hafnium wire with diameters ranging from 0.020" to 0.236".By utilizing advanced technologies, manufacturers can achieve higher levels of purity and performance in their hafnium wire products. This is particularly important for applications that operate under extreme conditions, such as high temperatures or corrosive environments. Advanced manufacturing techniques also enable the production of complex shapes and custom specifications, offering greater flexibility for specialized applications.
How to Verify the Purity and Composition of Hafnium Products
Verifying the purity and composition of hafnium products is essential for ensuring their quality and performance. One method of verification is through chemical analysis, which can detect the presence of impurities and confirm the material's composition. High-purity hafnium wire, like that produced by Youtian Metal, boasts a purity level of Hf+Zr>99.95%, ensuring minimal impurities and optimal performance.Other methods of verification include physical testing, such as tensile tests and ultrasonic testing (UT), which assess the material's mechanical properties and detect any internal flaws. These tests are conducted according to stringent quality requirements, providing confidence in the reliability and safety of the hafnium wire.
Case Studies: Customers Choosing Quality Hafnium Wire for Critical Applications
Several industries rely on high-quality hafnium wire for their critical applications. For example, the aerospace industry uses hafnium wire for its high melting point and corrosion resistance, making it ideal for components exposed to extreme temperatures. In the nuclear industry, hafnium wire is used in control rods due to its neutron-absorbing properties.One notable case study involves a leading aerospace manufacturer that chose Youtian Metal's hafnium wire for their high-temperature components. The wire's exceptional quality and performance contributed to the success of their project, demonstrating the importance of choosing a reliable hafnium wire supplier.Another case study highlights a nuclear reactor project where the use of high-purity hafnium wire ensured the safe and efficient operation of the control rods. The stringent quality control measures and advanced manufacturing techniques employed by Youtian Metal played a crucial role in meeting the project's demanding requirements.
In conclusion, the importance of quality control in hafnium wire production cannot be overstated. Strict quality standards, advanced manufacturing techniques, and rigorous verification methods are essential for producing reliable and high-performance hafnium wire. By choosing a reputable hafnium wire supplier like Youtian Metal, you can ensure the success and safety of your critical applications. Whether you're in the aerospace, nuclear, or any other industry that requires high-quality materials, investing in superior hafnium wire is a decision that pays off in the long run. Explore our offerings today and experience the difference that quality makes.
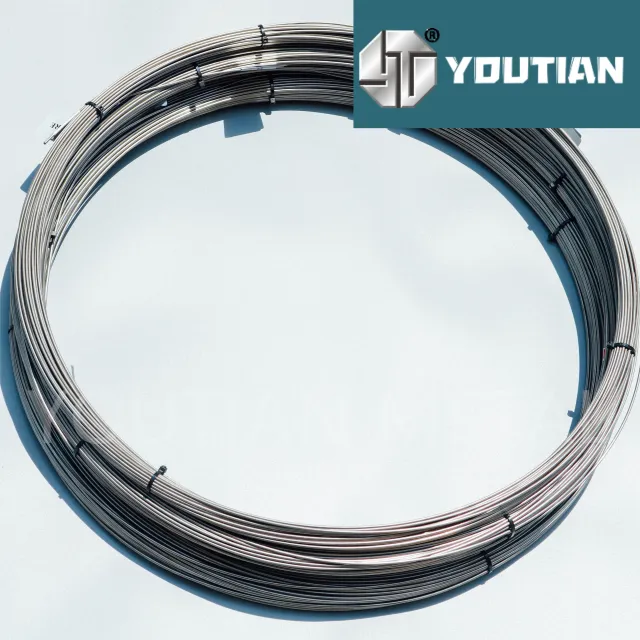
Comments
Post a Comment