In the world of non-destructive testing (NDT), magnetic flux leakage (MFL) stands as a pivotal technique that has revolutionized the way we detect flaws and imperfections in ferromagnetic materials. This advanced method enables industries to ensure the safety, integrity, and longevity of critical components without causing any damage.
Table of contents:
What is Magnetic Flux Leakage and How Does it Work?
Key Advantages of Using Magnetic Flux Leakage for Inspections
Comparing Magnetic Flux Leakage with Other NDT Methods
But what exactly is magnetic flux leakage detection, and how does it work its magic in the realm of NDT inspections? In this blog post, we'll unravel the mysteries of MFL, explore its key advantages, and compare it with other popular NDT methods to help you understand why it's becoming an industry favorite.
What is Magnetic Flux Leakage and How Does it Work?
Magnetic flux leakage is a sophisticated technique used to detect surface and sub-surface defects in ferromagnetic materials like steel pipes, plates, and bars. The process involves magnetizing the component under inspection and then analyzing the leakage field that occurs when there is a disruption in the uniform magnetic field, typically caused by flaws such as cracks or corrosion. This disruption creates a leakage field that can be detected using sensors, allowing for precise identification and analysis of the defect. The beauty of MFL lies in its ability to provide real-time results, enabling quick decision-making and corrective actions. The working principle of MFL is relatively straightforward yet highly effective. When a magnetic field is applied to a ferromagnetic material, it flows through the material uniformly. However, if there are any discontinuities or defects, such as a crack or a change in material thickness, the magnetic field is distorted, creating a leakage field. This leakage field can be detected using highly sensitive sensors, which then generate a signal indicating the presence and location of the defect. The data collected is often visualized in the form of a map or graph, making it easier for inspectors to identify and assess the severity of the flaw.
Key Advantages of Using Magnetic Flux Leakage for Inspections
The use of magnetic flux leakage in NDT inspections offers numerous advantages that set it apart from other testing methods. One of the primary benefits is its ability to provide accurate and reliable results in real-time. This immediacy is crucial in industries such as oil and gas, where timely detection of defects can prevent catastrophic failures and costly downtime. By offering on-the-spot results, MFL allows for swift decision-making and the implementation of corrective measures, ensuring the continued safety and efficiency of operations. Another significant advantage of MFL is its ability to detect both surface and sub-surface flaws. This dual capability makes it a versatile tool that can be used in a wide range of applications, from inspecting pipelines and storage tanks to assessing the condition of critical infrastructure components. The ability to detect sub-surface defects is particularly valuable in industries where hidden flaws can pose significant safety risks and lead to unexpected failures.
Comparing Magnetic Flux Leakage with Other NDT Methods
While magnetic flux leakage is a powerful tool, it's essential to compare it with other NDT methods to fully appreciate its strengths and limitations. One common alternative to MFL is ultrasonic testing (UT), which uses high-frequency sound waves to detect defects within materials. Ultrasonic testing is known for its ability to provide detailed information about the depth and size of defects, making it an excellent choice for certain applications. However, it can be more time-consuming and requires skilled operators to interpret the results accurately. Another popular NDT method is radiographic testing, which involves using X-rays or gamma rays to inspect the internal structure of a component. Radiographic testing is highly effective in detecting internal defects and can provide detailed images of the material's condition. However, it is more expensive and requires strict safety precautions due to the use of radiation.
In conclusion, magnetic flux leakage detection is a powerful and versatile NDT method that offers numerous advantages for industries that rely on the integrity of ferromagnetic components. Its ability to provide real-time, accurate results, detect both surface and sub-surface defects, and do so non-invasively makes it an invaluable tool for ensuring safety and reliability. By understanding the science behind MFL and investing in high-quality equipment from reputable manufacturers, companies can enhance their inspection processes, reduce maintenance costs, and ultimately, protect their assets and operations. Whether you're in the oil and gas, manufacturing, or infrastructure sector, magnetic flux leakage detection offers a practical and cost-effective solution for your NDT inspection needs.
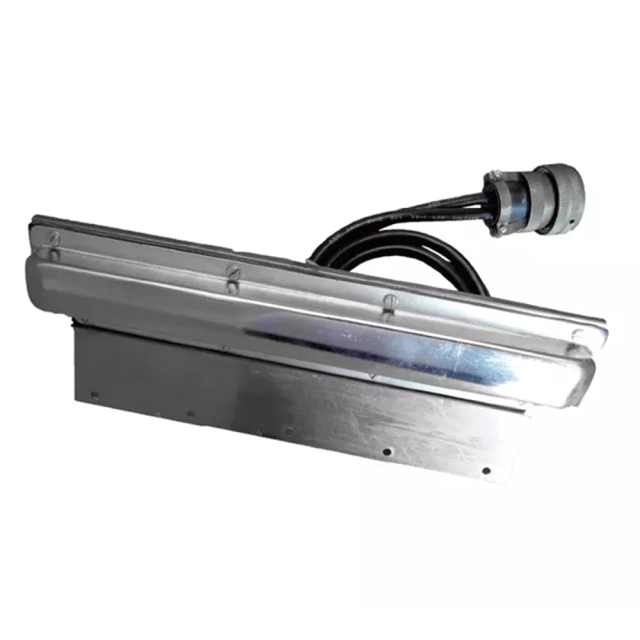
Comments
Post a Comment