The industrial landscape is evolving at a rapid pace, with granulation technology leading the charge in manufacturing efficiency and product quality. For those unfamiliar, granulation involves forming small particles from larger ones, a process vital in various industries. Innovations in granulator machine design are not just improving efficiency but also redefining how we approach manufacturing processes.
Table of contents:
Emerging Trends in Granulator Machine Design
The Role of Automation in Modern Granulation Processes
Tailoring Granulator Machines for Different Industries
This blog explores emerging trends in granulator machines, the role of automation, and how these technologies are tailored to meet the unique demands of different industries.
Emerging Trends in Granulator Machine Design
The evolution of granulator machines has been marked by notable innovations aimed at improving both functionality and efficiency. One of the most significant trends is the incorporation of high-vacuum technologies, such as those seen in Taeantech's high vacuum granulator machines. These machines use a vacuum degree of -100Kpa, ensuring that metals like gold, silver, and copper do not oxidize during the smelting process. This results in higher quality granules with no pores and no loss, making them ideal for use in premium applications. Another emerging trend is the development of machines that offer precise temperature control to ensure consistent quality. For instance, Taeantech's machines are equipped with a Mitsubishi PLC+PID temperature control panel, which maintains temperature accuracy within ±1°C. This level of precision is crucial for industries where material properties must be tightly controlled. Additionally, features like automatic frequency tracking make the melting process more stable and safer, ultimately boosting production efficiency.
The Role of Automation in Modern Granulation Processes
Automation is revolutionizing the way granulation processes are managed, offering numerous benefits such as increased efficiency, reduced labor costs, and minimized human error. One key example is the "one-click" operation feature in Taeantech's granulating machines, where the entire granulation process can be completed automatically. This not only simplifies operations but also ensures that the process is consistently reliable. Automated systems in granulation machines are increasingly being controlled by advanced software like Mitsubishi's human-machine interface. These systems allow for real-time monitoring and adjustments, ensuring optimal performance at all times. The integration of automated frequency tracking further enhances stability, leading to safer and more efficient operations. Furthermore, automation allows for seamless integration with other manufacturing processes. This is particularly beneficial for industries that require a continuous flow of materials, such as pharmaceuticals and chemicals. Automated granulation systems can be programmed to operate in unison with other machinery, thereby streamlining the entire production line and significantly boosting overall productivity.
Tailoring Granulator Machines for Different Industries
The versatility of granulator machines makes them suitable for a wide range of industries, from pharmaceuticals and chemicals to metallurgy and food processing. Each industry has unique requirements that necessitate specialized features in granulator machines. For instance, the pharmaceutical industry often requires granulation of active pharmaceutical ingredients (APIs) into uniform particles for better drug formulation. Machines with precise temperature control and vacuum capabilities are essential here to maintain the integrity of the APIs. In the metals and metallurgy industry, granulator machines are designed to handle high temperatures and various metal types. Taeantech's high-vacuum granulator machines, capable of reaching temperatures up to 1500°C, are perfect for granulating metals like gold, silver, and copper. These machines also feature multiple protection systems to safeguard against overcurrent, overvoltage, and other potential operational risks. The food processing industry, on the other hand, requires granulator machines that can produce food-grade granules. These machines must be easy to clean and maintain to meet stringent hygiene standards. Features like electromagnetic stirring and high-vacuum protection can also be beneficial in ensuring the quality and consistency of food products.
The advancements in granulator machine design and automation are setting new standards in various industries, from pharmaceuticals and chemicals to metallurgy and food processing. These machines are not only improving efficiency but also enhancing the quality of the final products. By incorporating high-vacuum technologies, precise temperature controls, and automated systems, granulator machines are becoming indispensable tools in modern manufacturing processes. For businesses looking to stay ahead in this competitive landscape, investing in advanced granulator machines is a strategic move. Companies like Taeantech are at the forefront of this innovation, offering state-of-the-art machines that cater to diverse industrial needs. If you're interested in exploring how these advancements can benefit your business, consider reaching out to a reputable granulator machine manufacturer for more information.
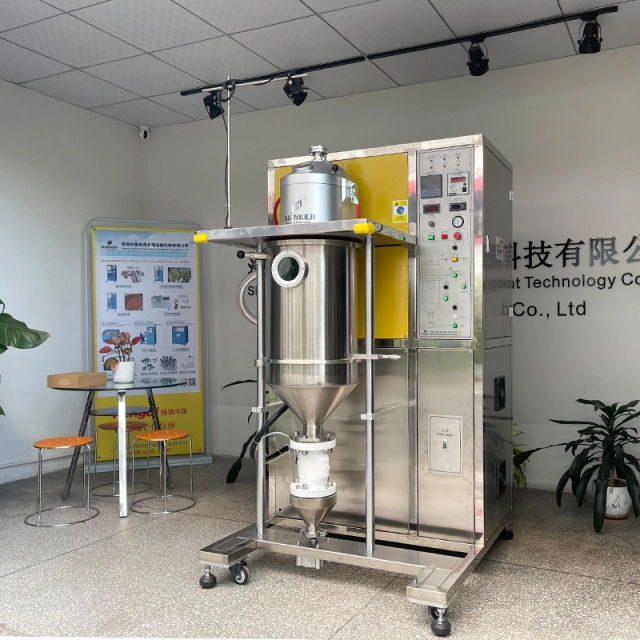
Comments
Post a Comment