In the realm of precision machining, the tools you choose can either make or break your projects. Among the myriad of options available, carbide end mills stand out as the champions of the trade. These tools have transformed the landscape of CNC machining, offering unmatched durability, precision, and efficiency. For professionals in the industry, understanding the profound impact and applications of carbide end mills is crucial. This article will unravel the essential reasons why carbide end mills are indispensable and guide you through their key features and benefits.
Table of content
The Advantages of Using Carbide End Mills in CNC Machining
How Carbide End Mills Deliver Superior Durability and Accuracy
Key Features to Look for in High-Quality Carbide End Mills
Why Carbide End Mills Are the Preferred Choice for Hard Materials
The Advantages of Using Carbide End Mills in CNC Machining
Carbide end mills have quickly become a staple in CNC machining due to their numerous advantages. One significant benefit is their exceptional heat resistance. Unlike traditional steel mills, carbide end mills can withstand higher temperatures, allowing for faster cutting speeds and reducing wear on the tool. This heat resilience translates into longer tool life, minimizing downtime for tool changes and maintaining productivity on the manufacturing floor.Additionally, carbide end mills provide superior surface finishes. Their rigidity and precision edge allow machinists to achieve smoother cuts with minimal chatter, which is particularly beneficial in applications requiring intricate detailing or high-tolerance finishes. This ability to produce a fine finish often reduces or eliminates the need for secondary finishing processes, saving time and resources.Lastly, carbide end mills are incredibly versatile. They can be used on a wide range of materials, from metals like steel and aluminum to composites and polymers. This versatility makes them a valuable tool for shops that work with diverse materials, ensuring that machinists always have the right tool for the job without needing an extensive inventory of specialized end mills.
How Carbide End Mills Deliver Superior Durability and Accuracy
At the heart of the carbide end mill's performance is its material composition. Made from a composite of tungsten carbide and cobalt, these tools offer a hardness that is significantly higher than high-speed steel (HSS) alternatives. This hardness provides exceptional wear resistance, allowing carbide tools to maintain their cutting edge even after prolonged use. The result is a more consistent and reliable performance over time.Furthermore, the precision manufacturing process of carbide end mills ensures unparalleled accuracy. Advanced production techniques, such as precision grinding and fluting, contribute to finer tolerances and meticulous geometric accuracy. This precision is crucial in CNC machining, where even the slightest deviation can lead to errors in the final product. With carbide end mills, machinists can trust that each tool will perform to exacting standards, maintaining the integrity of their projects.Another attribute contributing to the durability of carbide end mills is their reduced susceptibility to vibration. The rigidity of carbide as a material minimizes tool deflection, thereby decreasing the potential for vibration-induced inaccuracies. This stability is particularly advantageous when working with harder materials where tool deflection could lead to significant issues with dimensional accuracy.
Key Features to Look for in High-Quality Carbide End Mills
When selecting carbide end mills, there are several key features to consider to ensure high quality and optimal performance. Firstly, the flute design plays a critical role in chip evacuation and cutting efficiency. For instance, tools like the SHARPLY Original CNC Milling 5-Flute Carbide End Mill Cutter are engineered for high-performance precision cutting, making them ideal for various materials.The material composition is also paramount. High-quality carbide end mills use premium-grade tungsten carbide, which offers superior hardness and wear resistance. This ensures that the tool remains sharp and effective, even after extensive use. Additionally, look for end mills with a robust coating that can enhance performance by providing additional heat and wear resistance.Another important consideration is the size and geometry of the end mill. Depending on the specific application, you may require tools with different diameters, lengths, or ball nose tips for intricate detailing. Having a range of sizes available, such as those from SHARPLY that come in 4mm, 5mm, 6mm, and 8mm, ensures that machinists can tackle any project with confidence.
Why Carbide End Mills Are the Preferred Choice for Hard Materials
Carbide end mills are particularly favored for machining hard materials due to their unique properties. Their superior hardness allows them to cut through tough metals without losing their edge, making them ideal for projects involving hardened steels or exotic alloys. This capability is critical in industries such as aerospace or automotive manufacturing, where materials often have high tensile strength and require precise machining.The thermal stability of carbide end mills is another reason they excel with hard materials. High cutting speeds generate significant heat, which can damage tools and materials if not properly managed. Carbide's ability to maintain its mechanical properties at elevated temperatures enables efficient machining of hard materials without the risk of overheating.Finally, the precision and accuracy offered by carbide end mills make them indispensable for applications demanding tight tolerances. Whether it's creating complex geometries or achieving smooth surface finishes, these tools provide the reliability needed for high-stakes machining tasks. This accuracy ensures that even the toughest materials can be machined to exact specifications, reducing waste and rework.
In conclusion, carbide end mills are an essential tool in the arsenal of any precision machinist. Their durability, versatility, and precision make them the ideal choice for CNC machining applications across various industries. By investing in high-quality carbide end mills, professionals can achieve superior results, improve efficiency, and maintain a competitive edge in the market. For those looking to explore the full potential of carbide end mills, tools like the SHARPLY Original CNC Milling 5-Flute Carbide End Mill Cutter offer an excellent starting point, promising performance that meets the highest standards of excellence.
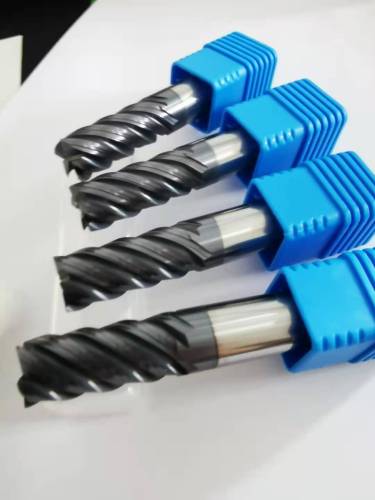
Comments
Post a Comment