In the world of textile manufacturing, the tools and components used can make a significant difference in the quality and efficiency of production. Among these essential components are circular knitting machine sinkers. These small yet mighty parts play a crucial role in the knitting process, ensuring that fabrics are produced seamlessly and efficiently. But what exactly makes high-quality sinkers so vital, especially in the context of sustainable textile manufacturing?
Table of contents:
The Role of Circular Knitting Machine Sinkers in Textile Manufacturing
How Premium Circular Knitting Machine Sinkers Contribute to Energy-Efficient Knitting Processes
Reducing Waste The Environmental Benefits of Durable Circular Knitting Machine Sinkers
This blog post explores the unique contributions of premium circular knitting machine sinkers, focusing on their impact on energy efficiency, waste reduction, and long-term cost savings. Whether you're a textile manufacturer or simply interested in sustainable practices, this guide will provide valuable insights into the importance of choosing the right knitting machine parts.
The Role of Circular Knitting Machine Sinkers in Textile Manufacturing
Circular knitting machines are the backbone of modern textile production, responsible for creating a variety of fabrics used in clothing, home textiles, and more. At the heart of these machines are sinkers, which are crucial for the loop formation process. A high-quality circular knitting machine sinker ensures that each loop is formed consistently, leading to smoother fabric textures and reducing the risk of defects. By maintaining precision in the knitting process, these sinkers help maximize machine efficiency and output. The choice of sinkers can greatly influence the overall performance of a circular knitting machine. Manufacturers that opt for superior quality sinkers, like those provided by trusted circular knitting machine sinker manufacturers, benefit from improved machine longevity and reduced downtime. The durability and resilience of top-notch sinkers mean they can withstand the demands of high-speed operation and complex patterns without compromising fabric quality. This reliability becomes especially important in a competitive industry where time is money.
How Premium Circular Knitting Machine Sinkers Contribute to Energy-Efficient Knitting Processes
In today's environmentally conscious world, energy efficiency is a top priority for manufacturers across various industries. Textile manufacturing, in particular, demands significant energy consumption, making it crucial to adopt practices and technologies that minimize energy use. High-quality circular knitting machine sinkers contribute to this goal by enhancing machine performance and reducing energy waste during operation. Premium sinkers are designed to offer smoother operation within the knitting machine, which translates to less friction and lower energy requirements. When knitting machines run more smoothly, they need less power to maintain optimal speeds and functions. This reduction in energy demand not only decreases operational costs but also lessens the carbon footprint of textile manufacturing facilities. In this way, investing in superior sinkers provides both economic and environmental benefits.
Reducing Waste The Environmental Benefits of Durable Circular Knitting Machine Sinkers
Sustainability in textile manufacturing goes beyond energy efficiency; it also encompasses waste reduction. One significant advantage of using durable circular knitting machine sinkers is their contribution to minimizing material waste. High-quality sinkers ensure that fabrics are knitted without defects, thereby reducing the amount of discarded material due to imperfections. This quality control is essential for manufacturers aiming to optimize resources and minimize waste. Long-lasting sinkers require less frequent replacement, which directly impacts the reduction of industrial waste. By choosing sinkers that endure prolonged use, manufacturers can lower their consumption of Circular Knitting Machine spare parts, leading to fewer discarded components. This reduction in waste aligns with the principles of the circular economy, where products are designed to last, and their end-of-life impact is minimized. Manufacturers committed to sustainability should prioritize the use of such durable parts in their operations.
In conclusion, the choice of sinkers used in circular knitting machines has a profound impact on both the operational efficiency and sustainability of textile manufacturing. High-quality circular knitting machine sinkers, sourced from reputable circular knitting machine sinker manufacturers, offer numerous benefits, including energy efficiency, waste reduction, and long-term cost savings. By enhancing machine performance and durability, these sinkers contribute to smoother operations and more sustainable practices. For textile manufacturers committed to achieving excellence and sustainability, investing in premium sinkers is a strategic decision. By prioritizing quality in their machine parts, manufacturers can optimize their processes, reduce environmental impact, and achieve significant cost savings. The advantages of high-performance sinkers extend beyond the production floor, influencing customer satisfaction and market competitiveness. To explore more about how quality sinkers can transform your textile manufacturing operations, consider reaching out to industry experts and suppliers for tailored solutions suited to your needs.
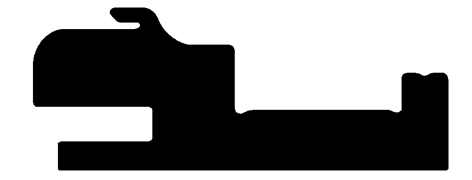
Comments
Post a Comment