In the world of manufacturing, precision and efficiency are key. Video measuring machine (VMMs) have revolutionized industries that rely on accurate and fast dimensional analysis. One of the standout features of these systems is non-contact measurement, a technology that allows for precise evaluation without physically touching the object. But why is this important, and what benefits does it offer to end users? Let’s dive into six key areas that make non-contact measurement essential for businesses.
Table of contents
Protection of Delicate Components
Protection of Delicate Components
One of the primary reasons manufacturers choose video measuring machines with non-contact capabilities is to safeguard delicate components. Many industries, such as electronics, medical devices, and aerospace, work with fragile parts that can be damaged by traditional contact-based measurement methods. Whether inspecting microchips, surgical tools, or turbine blades, VMMs provide an accurate, gentle alternative that ensures no physical force is applied during the measurement process. This is crucial for maintaining the integrity of intricate, sensitive parts.
High-Precision Measurements
Non-contact measurement allows for sub-micron precision, something that is difficult to achieve with manual or contact-based tools. By using high-resolution cameras and advanced software, VMMs can detect and measure features as small as a few microns. This level of precision is vital in industries like automotive and aerospace, where even minor deviations can impact the overall performance and safety of products. Geometric measurements, such as angles, radii, and complex shapes, can also be accurately captured without any physical interference.
Speed and Efficiency
In addition to precision, non-contact systems significantly improve inspection speed. Since there is no need to manually position or touch the part, VMMs can measure multiple points quickly, reducing overall inspection time. In industries where high-volume production is the norm, this speed is a game-changer. It allows manufacturers to increase throughput without sacrificing accuracy. For example, in medical device manufacturing, non-contact measurement helps ensure that large batches of products meet strict standards in a fraction of the time compared to traditional methods.
No Wear and Tear on Tools
One often overlooked benefit of non-contact measurement is the elimination of wear and tear on both the tools and the parts being measured. Traditional measurement techniques, especially those involving probes or calipers, can cause gradual damage to both the measuring instrument and the component, leading to inaccuracies over time. Non-contact systems, on the other hand, do not physically interact with the parts, meaning that the machine's accuracy is maintained for a longer period, and there’s no risk of scratching or distorting the object.
Environmental Independence
Non-contact measurement also shines in environments where traditional tools would struggle. For instance, in cases where the object being measured is sensitive to temperature changes, physical pressure, or deformation, non-contact methods ensure that no external force interferes with the measurement results. Materials that are prone to bending or warping under pressure, such as thin metal sheets or certain polymers, can be accurately measured without the risk of distortion, ensuring reliable data every time.
Increased Versatility
Finally, non-contact systems offer unmatched versatility. Whether the object has a complex shape, a reflective surface, or a combination of materials, VMMs can handle it all. They are adaptable to a wide range of industries, from measuring tiny electronic components to large aerospace parts. This versatility also extends to the type of data they collect, with some systems capable of both two-dimensional (2D) and three-dimensional (3D) measurements.
Non-contact measurement in video measuring machines is more than just a technological upgrade; it’s a necessity for industries that demand precision, speed, and versatility. From protecting fragile components to offering sub-micron accuracy and rapid measurements, VMMs equipped with non-contact technology ensure that manufacturers can maintain high-quality standards efficiently. To learn more about how video measuring machine can transform your quality control processes, visit Easson.
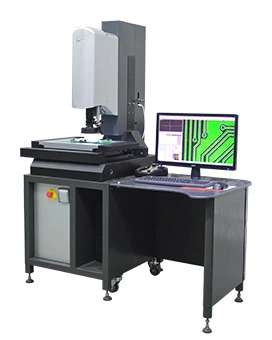
Comments
Post a Comment