Nickel alloys offer versatility, strength, and corrosion resistance that make them indispensable across various industries, from aerospace to healthcare. For businesses requiring efficiency and durability, working with the right nickel alloy supplier is paramount. With expertise in customizing materials to meet exact specifications, nickel alloy manufacturers can create tailor-made solutions that address precise industry challenges. Whether producing high-performance nickel alloy 718 or developing nickel chromium alloys, customized materials have become the backbone of innovation and efficiency in demanding sectors.
Table of contents:
Tailored Nickel Alloy Production for Aerospace and Defense
Benefits of Custom Nickel Alloy Components in Healthcare Equipment
Creating Nickel Chromium Alloy Solutions for Chemical Processing Plants
Key Considerations for Customizing Nickel Alloys
Tailored Nickel Alloy Production for Aerospace and Defense
The aerospace and defense industries rely on high-strength materials capable of withstanding extreme conditions. Custom nickel alloy production plays an integral role here. Nickel alloys like nickel alloy 718 are valued for their ability to endure high temperatures while maintaining structural integrity. This makes them ideal for applications such as gas turbines, jet engines, and rocket components. For instance, nickel chromium alloys exhibit superior oxidation resistance, a critical requirement in aerospace components exposed to intense heat. Additionally, aerospace-grade nickel alloys can be customized for weight-saving solutions without compromising strength. This is highly advantageous in an industry where every gram counts toward fuel efficiency and performance.
Benefits of Custom Nickel Alloy Components in Healthcare Equipment
Healthcare equipment demands materials that are biocompatible, corrosion-resistant, and capable of precision formability. Nickel alloys meet these needs with exceptional performance. Medical tools and implants often incorporate nickel chromium alloys for their ability to resist degradation from sterilization processes and bodily fluids. Custom components allow for meticulous tailoring to achieve the exact requirements of surgical and diagnostic tools. For example, nickel alloys can be used to manufacture MRI-compatible equipment, ensuring non-magnetic and corrosion-resistant properties without compromising imaging quality. Furthermore, the pharmaceutical industry benefits from custom-designed nickel alloy reactor vessels that withstand chemical exposure during drug production, offering increased durability and sterility.
Creating Nickel Chromium Alloy Solutions for Chemical Processing Plants
Chemical plants operate in aggressive environments where materials are exposed to corrosive agents, temperatures, and pressures. Custom nickel chromium alloys are commonly utilized in chemical processing equipment such as heat exchangers, reactors, and pumps. These alloys offer excellent resistance to harsh chemicals such as acids, alkalis, and chlorides, which are prevalent in the industry. By allowing customization, manufacturers can optimize alloys for specific applications, such as enhancing thermal conductivity for heat exchangers or increasing strength for pressurized reactors. A key benefit is the extended service life of the equipment, reducing maintenance downtime and overall costs for plant operators.
Key Considerations for Customizing Nickel Alloys
When customizing nickel alloys, several critical factors should be considered to maximize their performance and application. First, the precise composition of the alloy is essential. Nickel alloys can incorporate varying amounts of elements like chromium, molybdenum, and niobium to achieve specific characteristics such as high-temperature resistance or enhanced corrosion resistance. For instance, nickel alloy 718 is often tailored by adjusting heat treatment processes to improve its mechanical properties for aerospace applications. Second, industry requirements such as certifications and compliance with standards (e.g., ASTM, AMS) should guide customization. Aerospace and medical sectors, for example, have stringent quality and safety requirements that manufacturers must adhere to. Additionally, operational conditions such as temperature, pressure, and exposure to corrosive agents must dictate the choice of alloy characteristics.
Lastly, working with an experienced nickel alloy supplier ensures that customization is performed with precision and expertise. The collaboration between manufacturers and industries allows for creating nickel alloys that meet the unique demands of specialized environments.By integrating custom solutions into industry processes, businesses can unlock improved efficiency, reliability, and sustainability, bringing forth innovation and competitive advantage.
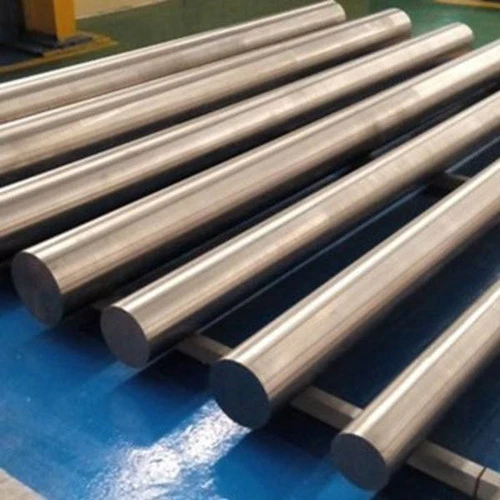
Comments
Post a Comment