Tailoring PMI foam to specific applications has become essential for modern industry, enabling manufacturers to meet unique demands across aviation, construction, automotive, and more. PMI foam, such as Rifeng W, offers unmatched structural versatility, lightweight properties, and adaptability in design, making it a preferred choice for numerous industries. By leveraging the benefits of custom production, PMI foam manufacturers are revolutionizing the way projects achieve both efficiency and performance.
Table of contents:
Benefits of Customizing PMI Foam for Specific Applications
Industries Benefiting from Custom PMI Foam Solutions
Process of Developing Custom PMI Foam Products
Challenges and Solutions in Custom PMI Foam Manufacturing
Benefits of Customizing PMI Foam for Specific Applications
The customization of PMI foam delivers a range of benefits that are essential for project-specific needs. Custom PMI foam products enable manufacturers to optimize the material's mechanical and thermal properties, such as improving tensile strength and heat resistance. This adaptability ensures better integration in applications ranging from aerospace components to underwater buoyancy materials. Manufacturers who specialize in custom production gain a competitive edge by providing tailored solutions that reduce excess material waste, enhance resin uptake efficiency, and create lighter yet robust structures. For example, Rifeng W, a renowned PMI foam, achieves significant weight savings due to its fine cell structure, which minimizes resin absorption during production processes. Such customization not only reduces costs but also improves environmental sustainability, which is increasingly vital in today’s industries.
Industries Benefiting from Custom PMI Foam Solutions
PMI foam has a broad spectrum of applications across multiple sectors, where its unique properties create exceptional advantages. The aerospace and aviation industry frequently utilize custom PMI foam cores such as Rifeng W due to their outstanding strength-to-weight ratios and ability to withstand curing temperatures up to 130°C or even 180°C after heat treatment. These qualities ensure optimal performance in aerospace composites, as well as radomes and UAV components. Within the automotive industry, lightweight PMI foam plays a crucial role in reducing vehicle weight, thereby improving fuel efficiency and contributing to lower emissions. Additionally, marine sectors benefit from its application in shipbuilding, where PMI foam combines lightweight properties with resistance to harsh environmental conditions like prolonged exposure to water. Even the healthcare sector, as reflected in Rifeng W's use in X-ray and CT table tops, experiences the advantages of this versatile core material. The PMI foam's adaptability provides groundbreaking solutions in industries as diverse as medical technology, wind turbine blades, and sports and leisure manufacturing.
Process of Developing Custom PMI Foam Products
The process of developing custom PMI foam exemplifies the innovation and technical precision required by advanced manufacturing. PMI foam manufacturers engage in intensive product development cycles to create foam cores that meet specific client requirements. Technology such as thermoforming and CNC machining enables manufacturers like Rifeng to produce pre-shaped and ready-to-use foam components with high precision. This ensures seamless integration into projects with simple or complex geometries. Additionally, advanced processes, including vacuum infusion and RTM technologies, allow refined resin distribution, demonstrating the foam's compatibility with intricate manufacturing methods. Heat treatment further enhances the foam's durability, expanding its application to industries requiring higher thermal and mechanical resistance. By tailoring foam sizes, densities, and properties, custom production PMI foam manufacturer deliver solutions that can adapt to any challenging design or functionality demand.
Challenges and Solutions in Custom PMI Foam Manufacturing
While the customization of PMI foam delivers unmatched advantages, it also involves distinct challenges. Custom production requires balancing performance and cost concerns, as high-quality PMI foam and precision machining can increase initial production expenses. Another critical hurdle is ensuring uniformity and consistency during foam density adjustments or advanced processes like infusion and heat treatment. Solutions to these challenges lie in the expertise of reputable PMI foam manufacturers, such as Rifeng. With innovative tools and machining capabilities, Rifeng can meet tight tolerance demands and deliver foam sheets in precise dimensions and geometries. Furthermore, their use of sustainable approaches in manufacturing addresses environmental concerns, enhancing the product's eco-friendliness without compromising performance. Through a combination of state-of-the-art technologies and material engineering, these challenges are consistently met with success, ensuring PMI foam serves its diverse applications effectively.
The adaptability of PMI foam highlights its integral role in shaping modern industries. From weight savings and increased efficiency to tailored mechanical properties, custom production delivers exceptional value across various applications. For businesses seeking innovative solutions, collaborating with trusted PMI foam manufacturers, such as Rifeng, provides the reliability and expertise required for groundbreaking projects. Whether it is creating lightweight vehicle components, advanced medical equipment, or aerospace composites, PMI foam offers endless possibilities for industrial innovation. Explore how Rifeng PMI foam can transform your project’s efficiency, functionality, and sustainability today.
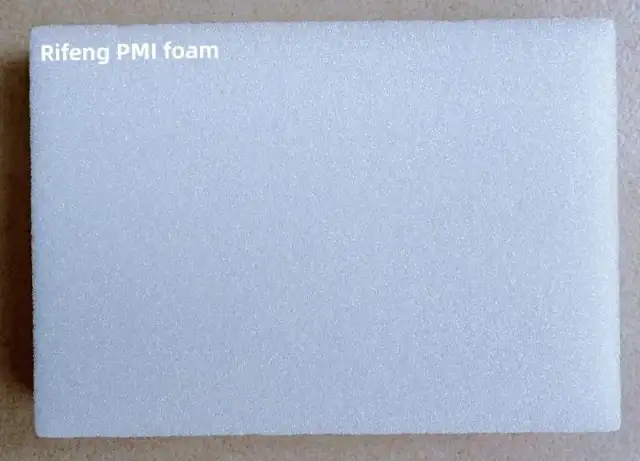
Comments
Post a Comment