Cemented carbide components have become a crucial material in industries requiring high durability, precision, and efficiency. From cutting tools to automotive manufacturing, the versatility of these components is unmatched. But selecting the right cemented carbide inserts or components for your specific application can feel overwhelming given the many options available. This guide will walk you through how to make the right decision with confidence.
Table of contents:
Factors to Consider When Choosing Cemented Carbide Grades
Customizing Cemented Carbide Components for Specific Needs
Evaluating Supplier Quality and Reliability
Case Studies: Successful Implementation of Cemented Carbide Solutions
Factors to Consider When Choosing Cemented Carbide Grades
One of the first steps in selecting cemented carbide components is understanding the grades. Cemented carbide grades differ based on the binder content, tungsten carbide particle size, and hardness. Applications that involve heavy wear and tear, such as mining tools, demand highly wear-resistant grades, while machining operations may require grades with a balance between toughness and resistance. Assess your industry needs carefully and match the grade of cemented carbide to the specific use case. Factors like machining speed, surface finish requirements, and material being worked on also come into play when making this decision.
Customizing Cemented Carbide Components for Specific Needs
Customizability is one of the most appealing aspects of using cemented carbide inserts. Many manufacturers offer tailored solutions to meet the precise demands of your operation. For example, advanced tools like the SHARPLY Tube Scraper Inserts use high-grade coating technologies (CVD and PVD) that enhance wear resistance and extend tool life. If your application spans multiple use cases—like handling varied tube diameters or working in high-speed production—requesting custom cemented carbide components can reduce inefficiency. Additionally, customization allows businesses to select optimized dimensions, geometries, and surface finishes to achieve maximum performance.
Evaluating Supplier Quality and Reliability
Choosing the right supplier for your cemented carbide inserts is just as important as picking the components themselves. Start by researching suppliers known for precision engineering and well-established industry credibility. Consider manufacturers like SHARPLY, who provide advanced tungsten carbide solutions while offering excellent technical support. It's essential to confirm the supplier’s adherence to stringent quality control processes, as misaligned standards can disrupt your production. Look for suppliers that provide detailed technical data sheets, have responsive communication, and deliver on promises of timely supply.
Case Studies: Successful Implementation of Cemented Carbide Solutions
Real-world examples highlight the effectiveness of cemented carbide components. For instance, SHARPLY’s Tube Scraper Inserts, which feature advanced coating technology, are used in professional tube and pipe production. These inserts remove rust and imperfections with remarkable precision, optimizing tool life and reducing downtime. Another success story can be seen in mining operations, where tough grades of cemented carbide withstand the abrasive environments, significantly increasing productivity. When making a selection, understanding how other companies successfully implemented cemented carbide components in similar contexts can guide your choice.
Selecting the right cemented carbide components is essential to achieving operational efficiency, enhancing product performance, and staying competitive in your industry. By considering key factors like grade selection, customization options, and supplier reputation, you can confidently make decisions that impact your business positively. A well-chosen cemented carbide solution will not only boost your productivity but also reduce long-term costs by minimizing replacements and downtimes.
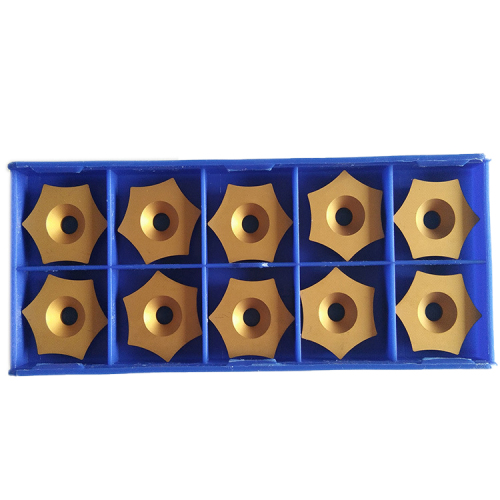
Comments
Post a Comment