The field of cemented carbide manufacturing has seen remarkable advancements, making it a crucial material for industrial applications. From cutting tools and high-performance inserts to specialized components for demanding environments, cemented carbide plays a pivotal role in modern industry. This article explores the innovative techniques revolutionizing cemented carbide production, focusing on advancements in sintering, the impact of nanostructuring, additive manufacturing, and future trends that are shaping the industry.
Table of contents:
Advancements in Sintering Processes for Cemented Carbide
The Impact of Nanostructuring on Cemented Carbide Properties
Additive Manufacturing: 3D Printing of Cemented Carbide Components
Future Trends in Cemented Carbide Production
Advancements in Sintering Processes for Cemented Carbide
One of the most critical steps in cemented carbide production is the sintering process, which influences the material's hardness, toughness, and wear resistance. Recent innovations in sintering technology have greatly improved the quality and performance of cemented carbide components. High-pressure sintering (HPS) and Hot Isostatic Pressing (HIP), for example, have become widely adopted techniques to enhance material density and eliminate porosity, ensuring consistent properties across the component. Furthermore, controlled atmosphere sintering has allowed manufacturers to fine-tune the microstructure of cemented carbide inserts, leading to superior mechanical properties and longer tool life. These advancements not only enhance product performance but also reduce overall manufacturing costs, making high-quality cemented carbide products more accessible.
The Impact of Nanostructuring on Cemented Carbide Properties
Nanostructuring has emerged as a game-changing approach in improving the properties of cemented carbide components. By reducing the grain size of the material to the nanometer scale, manufacturers can achieve a unique balance of hardness and toughness. Nanostructured cemented carbide offers superior wear resistance, making it ideal for high-performance cutting tools and industrial applications. Additionally, smaller grain sizes result in a more uniform distribution of binder phases, leading to improved fracture toughness. Nanostructuring also opens up possibilities for incorporating advanced coatings, further enhancing the durability and functionality of cemented carbide inserts. This innovative approach has significant implications for industries ranging from aerospace to automotive, where performance and reliability are paramount.
Additive Manufacturing: 3D Printing of Cemented Carbide Components
The rise of additive manufacturing, commonly known as 3D printing, has brought a revolution to the production of cemented carbide components. Traditional manufacturing methods often involve significant material wastage and complex machining processes. Additive manufacturing, however, allows for near-net-shape production, minimizing material loss and enabling intricate geometries that were previously unattainable. Powder bed fusion and binder jetting are two popular techniques for 3D printing cemented carbide parts. These methods offer excellent precision, flexibility, and scalability, making them suitable for a wide range of applications. While still in its early stages, the integration of additive manufacturing with advanced coating technologies, such as those used in SHARPLY Tube Scraper Inserts, further enhances the potential of 3D-printed cemented carbide products. This technology promises to redefine the manufacturing landscape, offering faster production cycles and unlocking new design possibilities for cemented carbide inserts and other components.
Future Trends in Cemented Carbide Production
The future of cemented carbide production is poised for continued transformation, driven by technological advancements and evolving industry demands. Advanced coating technologies, such as Chemical Vapor Deposition (CVD) and Physical Vapor Deposition (PVD), are expected to play a more prominent role in enhancing the wear resistance and heat protection of cemented carbide inserts. Sustainability is another key trend, with manufacturers focusing on recycling initiatives and the use of alternative binders to reduce environmental impact. Furthermore, the integration of artificial intelligence (AI) and machine learning in manufacturing processes is anticipated to optimize production parameters, ensuring consistent quality and performance. The adoption of smart manufacturing practices, such as the Internet of Things (IoT) and real-time monitoring, will also contribute to greater efficiency and reduced downtime. These trends underscore the importance of innovation in maintaining the competitiveness and relevance of cemented carbide in a dynamic industrial landscape.
From advancements in sintering and nanostructuring to the potential of additive manufacturing, the innovations in cemented carbide manufacturing techniques are shaping the future of industrial solutions. These developments enable the creation of superior tools and components that cater to the demands of modern industries. For businesses seeking high-performance cemented carbide inserts or components, partnering with forward-thinking manufacturers is crucial. Explore SHARPLY's advanced offerings to discover cutting-edge solutions designed to meet the challenges of today's industrial applications.
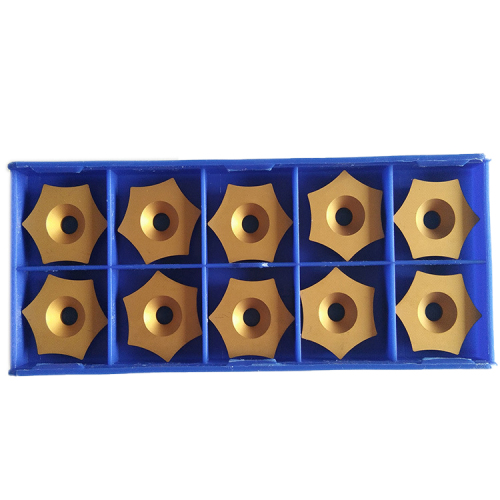
Comments
Post a Comment