The manufacturing industry has seen groundbreaking advancements over the years, and the evolution of heat press machine is no exception. These machines have transitioned from basic tools to state-of-the-art equipment integral to modern industrial processes. Heat press machines, particularly the hot forming press and hot pressing machine, have become indispensable in shaping, molding, and forming materials with precision and efficiency. This blog explores key innovations, the impact of automation, comparisons of traditional and modern machines, and what the future holds for heat press technology.
Table of contents:
Innovations That Are Redefining Modern Hot Forming Press Technology
How Automated Heat Press Machines Improve Production Speeds
A Comparison Between Traditional and Servo-Electric Hot Pressing Machines
Trends in Hot Forming Press Design for Future Industries
Innovations That Are Redefining Modern Hot Forming Press Technology
Today's hot forming press machines are marvels of engineering, incorporating cutting-edge features that enhance their functionality and effectiveness. Innovations such as precision machining frames and compartmentalized heating systems allow for unparalleled accuracy. For example, technologies like servo-electric hot press machines feature high-temperature capabilities that improve material forming with smaller tonnage requirements and minimal deformation. Additionally, advancements in temperature control and parallelism have become game-changers in achieving uniformity and reducing errors. A prime example is the MEA Servo-electric hot forming press, which uses a superlative control system to deliver precision and efficiency.
How Automated Heat Press Machines Improve Production Speeds
Automation has revolutionized the capabilities of heat press machines, significantly improving production speeds and operational efficiency. Modern automated systems, such as the servo-electric hot pressing machine, enable businesses to handle repetitive tasks with ease, ensuring precision control and consistent results. Automated systems also allow for optimized pressure, temperature, and time settings, which speeds up manufacturing processes and reduces downtime. Features like PLC control systems and digital displays in machines such as the fuel cell MEA Servo-electric hot forming press further enhance operational accuracy. By integrating automation, industries can produce complex components like automobile parts and high-temperature molded materials efficiently and at scale.
A Comparison Between Traditional and Servo-Electric Hot Pressing Machines
The transition from traditional to servo-electric hot pressing machines marks a pivotal shift in manufacturing technologies. Traditional hot forming presses relied on hydraulic systems, which, while effective, often lacked precision and generated significant noise and vibration. On the other hand, servo-electric machines provide a quieter and more controlled solution. For instance, machines like the MEA Servo-electric hot press offer remarkable stroke control accuracy, as well as stroke repetition within 0.1mm. This advancement ensures enhanced performance and reduced operational errors. Additionally, servo-electric machines offer energy savings and superior adaptability for producing intricate parts, making them ideal for industries requiring high precision and efficiency.
Trends in Hot Forming Press Design for Future Industries
The design of modern hot forming press machines continues to evolve, driven by the demands of future industries. Environmentally conscious manufacturing practices are leading to the adoption of energy-efficient and sustainable machines. Advanced materials engineering and adaptive controls are enabling manufacturers to produce more complex and efficient designs. Machines like the MEA Servo-electric hot forming press are already paving the way with features such as low-temperature pressing procedures and compact, high-efficiency frames. Furthermore, the integration of AI and IoT is expected to reshape hot pressing machines by enabling predictive maintenance, remote monitoring, and even greater levels of customization for diverse industry needs.
The advancements in hot forming press technology are shaping the future of manufacturing by prioritizing precision, efficiency, and sustainability. With innovations like servo-electric machines, adaptive controls, and AI integration, industries can meet the increasing demand for complex and high-quality components while reducing environmental impact. These forward-thinking designs ensure that manufacturers stay competitive and responsive in a rapidly evolving industrial landscape. Continuing to invest in such technological progress will undoubtedly drive the industry toward a more efficient and sustainable future.
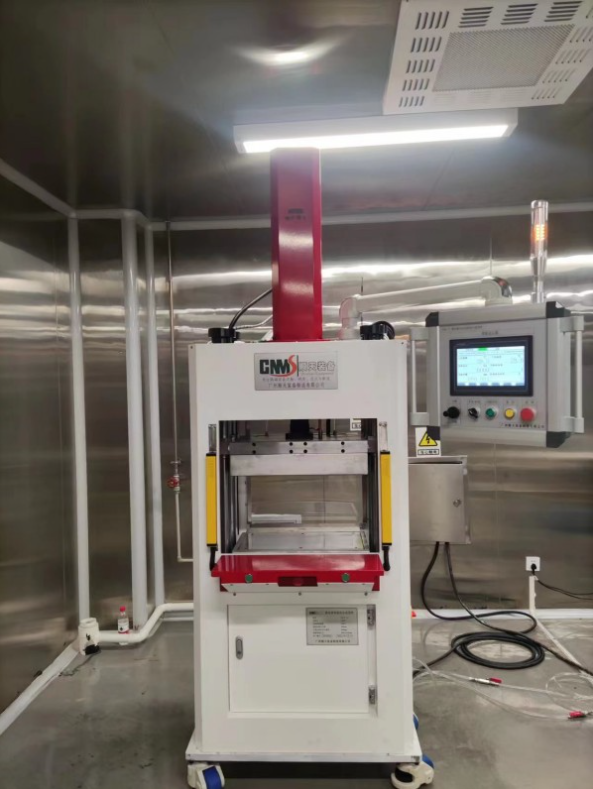
Comments
Post a Comment