Table of contents:
The Differences Between Electroless and Acid Zinc Plating
Advantages of Electroless Zinc Plating in Certain Applications
How Acid Zinc Plating Offers Faster and More Cost-Effective Solutions
The Differences Between Electroless and Acid Zinc Plating
Electroless zinc plating is a chemical process that deposits a uniform layer of zinc onto a substrate without the use of electricity. This makes it ideal for complex shapes and recessed areas where achieving uniform coverage with electroplating can be challenging. In contrast, acid zinc plating, a common form of zinc plating, is an electroplating process that utilizes an electric current to deposit zinc ions from an acidic electrolyte solution onto the metal part. The electrolyte often contains zinc plating intermediates, which act as brighteners and levelers, influencing the deposit's appearance and performance. The primary difference lies in the method of deposition: chemical reaction versus electrochemical reaction. This difference significantly impacts the coating's uniformity, deposition rate, and overall cost.
Advantages of Electroless Zinc Plating in Certain Applications
Electroless zinc plating shines in applications requiring exceptionally uniform coating thickness, regardless of the component's geometry. This process is particularly beneficial for intricate parts or internal surfaces that are difficult to reach with traditional electroplating methods. The absence of an electric field ensures a consistent zinc layer even in recessed areas and blind holes, providing superior corrosion protection in these otherwise vulnerable locations. While the deposition rate might be slower and the process generally more expensive than acid zinc plating, the superior coverage and reduced risk of edge buildup often justify the cost for specialized applications demanding the highest level of corrosion resistance.
How Acid Zinc Plating Offers Faster and More Cost-Effective Solutions
Acid zinc plating, leveraging electrochemical deposition, typically boasts a faster deposition rate and lower operational costs compared to electroless zinc plating. This makes it a popular choice for high-volume production where speed and cost-effectiveness are paramount. The ability to deposit zinc rapidly onto a large surface area translates to significant savings in both time and resources. Moreover, with the right zinc plating intermediates and bath chemistry, acid zinc plating can achieve excellent brightness and leveling, creating an aesthetically pleasing and protective coating. While it may not offer the same level of uniformity as electroless plating on complex geometries, acid zinc plating provides a robust and economical solution for a wide range of applications, including automotive components, fasteners, and general hardware.
In conclusion, both electroless zinc plating and acid zinc plating are valuable methods for protecting metal parts from corrosion. Electroless plating offers unparalleled uniformity and coverage for complex shapes, while acid zinc plating provides a faster and more cost-effective solution for high-volume applications. By carefully considering your specific requirements, including part geometry, production volume, and budget, you can select the plating method that best meets your needs and ensures the long-term durability of your metal components. Choosing the right method will contribute greatly to the longevity of your product.
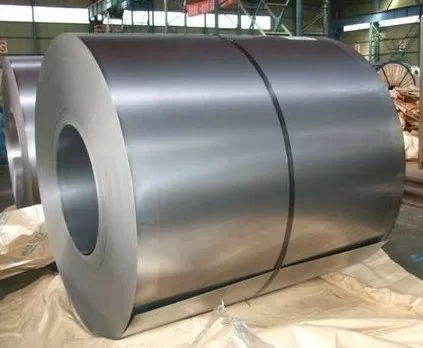
Comments
Post a Comment